인도 MIM 회사 소개
MIM 과정
Capabilities
Industries
Our Successes
News & Events
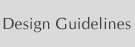
오늘날 금속사출성형은 자동차, 항공우주, 방위산업, 생활가전, 치과 임플란트 및 치과용구, 전자, 광섬유 컨넥터, 기밀용기, 외과용 의료장비와 임플란트, 전기 및 수공구 부품, 스포츠 장비 및 기타의 하드웨어 부품 등이 포함된 산업의 넓은 범위에서 극한적인 성능에 응용되어 적용되어 지고 있습니다.
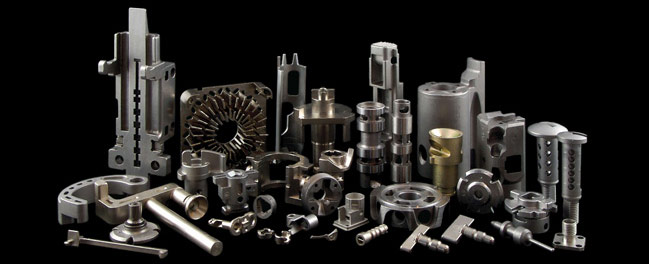
금속사출성형에 가장 적합한 부품은 통상 다음과 같은 특성을 지닌 것들이 유리합니다.
복잡한 것: 금속사출성형은 대부분 형상에 무제한적인 플라스틱 사출과 같이 제품 디자인에 있어 형태에 제약을 받지 않습니다. 왜냐하면 MIM은 틀에 의해 이루어지는 성형 공정이기 때문입니다. 그러므로 부가된 제품 형상에 비용의 추가가 이루어지지 않습니다. 이것은 밈에 의해 다기능 부품이 생산 가능하므로 각 부분 형상의 개별 부품 조립을 위한 가장 이상적인 방법입니다. 설계방식은 플라스틱 사출성형과 매우 유사하므로 대부분의 부품에 대해 쉽게 적용 가능합니다.
정밀도: 최종 형상에 대한 밈 정밀도에 대한 일반적인 가이드라인은 치수 기준 통상 +/-0.5%특성을 보입니다. 경우에 따라서는 최종 형상에 대해 +/-0.3%정도도 제작 가능합니다. 어떠한 경우에 있어서는 높은 정밀도의 제품에 있어 가능하다면 공차 완화를 하는 것이 비용적인 측면에서 바람직합니다. 밈 공정 단독으로 만족되지 못하는 공차는 다양한 후처리 공정을 통하여 만족하게 처리할 수 있습니다.
무게 및 크기: 밈은 100gr이하 중량 부품에 적당하나 가장 경제적으로 장점을 갖기 위해서는 50gr이하의 부품이 최적입니다. 최대 250gr까지의 부품에 적용할 수 있습니다. 밈 공정에서는 원재로 비용이 전체에서 차지하는 비용 중 가장 크게 차지합니다. 그러므로 가능하면 제품 중량을 절감하는 독창적인 방법이 장려됩니다. 플라스틱과 같이 중공(코아)또는 빗살대기(리브)등을 사용하여 제품 형상에 문제가 되지 않도록 중량을 절감할 수 있습니다. 밈은 0.1gr이하의 중량을 갖는 극단적으로 작은 마이크로 사이즈의 부품 생산에 최적의 방법입니다. 중량이 밈에 있어서 제한적인 인자는 아니며 길이에 있어서도 250mm정도까지 가능합니다.
절단면 두께: 밈에 있어 가장 적당한 벽 두께는 6mm이하가 좋습니다. 보다 두꺼운 것도 가능하지만 추가되는 재료비 및 보다 길어지는 공정시간으로 인해 비용 상승이 발생합니다. 반대로 0.5mm이하 매우 얇은 영역도 밈에 의해 가능합니다. 그러나 이 경우에는 설계에 많은 비중을 의존해야만 합니다.
생산량: 밈은 연간 수천 개에서 수백 만개에 이르기까지 생산 수량에 있어 경제적으로 생산할 수 있는 매우 유연한 공정입니다. 주조 및 플라스틱 공정처럼 툴링(금형제작)과 엔지니어링(시험사출작업, 시험양산작업 등)에 대한 초기 투자가 필요하며 볼륨이 적은 부분에 있어서는 일반적으로 의사 결정에 있어 강요되는 부분으로 작용합니다.
재질: 밈에 있어 재질은 철계 합금, 초합금, 티타늄 합금, 동합금, 내열합금, 결합탄화물합금, 세라믹과 금속기지 복합재료 등에 광범위하게 적용 가능합니다. 알미뉼이나 황동 등의 비철금속 합금에 대해서도 기술적으로는 가능하나 다이 캐스팅이나 기계가공 등의 다른 제조 공정이 일반적으로 보다 더 경제적인 방법입니다. 추가 정보를 통해 당사의 재질 부분에 대해서는 확인 바랍니다.
적용지원: 당사는 밈 공정에 대해 가장 높은 가치를 부여하기 위해 다양한 지원을 제공합니다. 기존 제품의 밈으로의 전환을 돕기 위해 양쪽(기준 설계와 밈 설계)설계에 대한 변환과 재료의 선정 및 FEA, 프로토제작 및 레이저 스캐닝등을 활용 시양산을 포함한 개발과 관계된 전 범위에 걸친 개발용역 등의 서비스 제공이 가능합니다.