Indo-MIM hakkında
MIM Prosesleri
Yetenekler
Endüstri
Başarılarımız
Haberler ve Etkinlikler
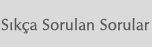
1. MIM teknolojisi nedir?
2. MIM teknolojisi nasıl uygulanır?
3. Kalıplama prosesinde metal ergiyor mu?
4. MIM ile geleneksel sinterleme prosesi arasındaki fark nedir?
5. Bağlayıcıların uzaklaştırılması esnasında parça çekiyor mu?
6. MIM parça mukavemeti ve yoğunluğu ne olacaktır?
7. Niçin MIM kullanmalıyım?
8. Hangi malzemeler üretilebilir?
9. MIM’den kazanç sağlayabilmek için hangi yol en iyisidir?
10. MIM için teslim süresi ne kadardır?
11. MIM için yıllık sipariş miktarı ne olmalıdır?
12. Karmaşıklığı belirlemek için bir kural var mıdır?
13. MIM de herhangi bir sınırlama var mıdır?
14. MIM’de ulaşılabilecek toleranslar nedir?
15. MIM proseslerinde ne tür ekipmanlar kullanılır?
16. MIM parçalara Isıl işlem ve kaplama yapılabilir mi?
MIM (Metal Enjeksiyon Kalıplama) Plastik Enjeksiyon Kalıplamanın kompleks parça üretim esnekliğiyle toz metalurjisinin çeşitli malzeme kullanma kabiliyetini birleştiren bir üretim teknolojisidir.

İnce metal tozları, termoplastik ve mum bağlayıcılarla karıştırılarak ham madde formuna getirilir. Ham madde ısıtıldığında kıvamlı bir akışkan haline getirilir ve yüksek basınç altında parça şeklinde hazırlanan mühendislik kalıbının içerisine basılır. Soğutmadan sonra parça kalıptan çıkarılır ve bağlayıcıların uzaklaştırılma prosesine alınır. Son aşama (sinterleme) ise yüksek sıcaklıkta kontrollü atmosfer altında metal taneciklerinin kendi aralarında kaynayarak tamamen yoğun olarak katılaşmasının sağlanmasıdır.
Hayır, sadece bağlayıcılar metal tozlarının, plastik malzeme gibi akışına izin vermek için ergitiliyor. Bağlayıcıların soğutulmasından sonra oluşan katılık, parçaya taşınabilme imkanı veriyor. Daha sonra parça, yüksek yoğunluk ve istenen mekanik özelliklere ulaşmak için sinterlenmek zorundadır.
Geleneksel sinterlemede, orta karmaşıklıktaki parçaları üretmek için, kalıp içersindeki büyük taneli metal tozlarına yüksek ve farklı eksenlerdeki basınç uygulanır. Tipik sinterleme prosesinde yoğunluk artışı sağlanamaz. Bu metodla ulaşılabilen yoğunluk aralığı, tipik olarak söz konusu alaşım için verilen teorik yoğunluğun %80-90 dır. MIM ürünlerde ise enjeksiyon kalıplama prosesinin esnekliğinden ve kompleks şekillerinden dolayı herhangi bir kısıtlama yoktur. Kullanılan ince metal tozları, yüksek sinterleme sıcaklığıyla birleştiğinde MIM’e, nihai üründe tam yoğunluğa ulaşılmasına izin verir. Bu, MIM ürünlerin, dövme malzeme özelliklerine benzer bir özellik kazanmasını sağlar.

Hayır, bağlayıcıların uzaklaştırılması prosesinde parça şekilsel olarak değişmiyor. Sinterleme ile tam yoğunluğuna ulaştığı için, parça sinterleme sonrasında şekilsel olarak yaklaşık %20 küçülüyor.
Tipik MIM yoğunluğu ≤ teorik yoğunluğun %96’sı. Dövme malzemede olduğu gibi teknik özellikler seçilen alaşım cinsine bağlı olarak değişkenlik gösterir.
Geleneksel talaşlı imalat ya da döküm teknolojileriyle üretilmesi zor ve pahalı olan küçük, çok karmaşık parçaların üretilmesinde MIM mükemmel bir çözümdür.
MIM prosseslerinde, hemen hemen her çeşit metal alaşımı kullanılabilir. Tipik olarak bu alaşımlar; yüksek mukavemet çelikleri, paslanmaz çelikler, ilave olarak nikel ve kobaltlı super alaşımlardır. Diğer işlenebilen malzemeler ise, refrakter metaller, titanyum ve bakır alaşımlarını kapsamaktadır. Pirinç, bronz, çinko ve alüminyum gibi düşük ergime noktasına sahip alaşımların kullanılması da mümkündür fakat genel olarak MIM prosesleri için ekonomik değildir. MIM proseslerindeki tüm malzemeler için Indo-MIM Malzeme Seçim Tablosuna bakınız.
MIM’den kazanç sağlamanın en etkin yolu, ilk tasarım, yani ürün geliştirme aşamasında bu teknolojiyi uygulamaktır. Mevcut metal şekillendirme teknolojisiyle üretmekte olduğunuz ya da üretmeyi düşündüğünüz yeni bir MIM komponentte Indo-MIM size destek sağlayacaktır.

Kalıp ve ilk numune için ortalama teslim süresi 8-10 haftadır. Fakat, özel proje gereksinimlerine bağlı olarak bunu kısaltmak mümkündür.
Genel olarak, yıllık üretim hacmi 20.000 adetin üstünde olan parçalar için uygundur. Bununla birlikte, müşterimizin bundan farklı yıllık üretim hacimlerinin ekonomik olup olmadığını Indo-MIM’e danışması gerekiyor.
Burada doğru ve yanlış yoktur. Temel kural, eğer çizimde 20'den fazla kritik ölçü varsa - bu parça MIM için uygun bir parçadır.
Her teknoloji de olduğu gibi MIM’ de de sınırlamalar vardır. Yaklaşık ürün ağırlığı 240 gramı geçmemelidir (en ekonomik üretim 50 gram ağırlığa kadar olamasına rağmen). Bazı geometrik özellikler de bir sorun olabilir (örneğin son derece ince ya da kalın kesitler gibi) Indo-MIM gereksinimlerinize göre en uygun tasarım seçenekleri için tavsiyede bulunur.
Tipik olarak MIM toleransları boyutun ±% 0,03 - 0.05 ‘i arasındadır. Ancak, toleranslar yüksek oranda ürün geometrisine bağlıdır. MIM prosesi ile ulaşılamayan toleranslara, daha sonra uygulanan makina operasyonları ile ulaşılır. Indo-MIM sizin ihtiyaçlarınızı karşılayan ürünü temin için, kendi tesislerindeki diğer üretim olanaklarını da kullanır.

MIM teknolojisinde özel donanımlı makinalar kullanır. En iyi proses çıktılarını alabilmek için, Indo-MIM,en son kontrol sistemlerine haiz gelişmiş makinaları kullanır. Indo-MIM, bir çok ABD ve Avrupalı makina imalatçıları ile yaptığı stratejik işbirliği sonucunda, makinalarını özel talepleri doğrultusunda inşa ettirmiştir.
Evet, MIM parçalara da, döküm veya dövme ürünlere uygulanabilen ısıl işlem ve kaplama uygulaması yapılabilir. Indo-MIM, kendi tesislerinde bulunan ısıl işlem ve kaplama tesisleriyle tamamen bitmiş ürün tedarik etmektedir.