Indo-MIM hakkında
MIM Prosesleri
Yetenekler
Endüstri
Başarılarımız
Haberler ve Etkinlikler
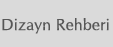
MIM bugün, otomotiv, havacılık ve savunma, tüketim elektroniği, diş hekimliği implantları ve aletleri, elektronik ve fiber optik bağlantılar, hermetik paketler, cerrahi aletler ve implantlar, endüstriyel takımlar, elektrikli el aletleri ve spor ekipmanları gibi çok geniş bir yelpazedeki endüstride kritik performans istenen parçaların üretiminde kullanılmaktadır.
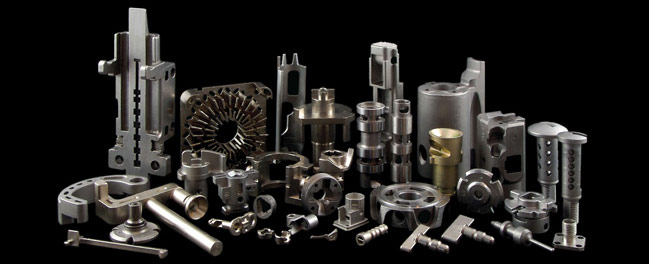
Genellikle MIM için uygun ürünler aşağıdaki özelliklere sahiptir
Komplekslik: Plastik enjeksiyonda bulunan neredeyse kısıtlamasız yüzey elde etme dizayn özgürlüğü, aynen MIM’de de bulunmaktadır. MIM’ de bir kalıplama prosesi olduğu için, çok fonksiyon istenen ürünleri oluşturan parçaların, ilave ürün özellikleri maliyeti artırmaz, bundan dolayı da MIM ideal bir çözümdür. MIM dizayn kuralları, plastik enjeksiyon kalıplama kurallarına çok yakındır, bundan dolayı, çoğunlukla tüm ürünlere uygulanması kolaydır.
Hassasiyet: MIM hassasiyeti için genel prensip; tolerans, boyutun ± % 0.5 ‘i şeklindedir. Bazı durumlarda ± % 0.3 ‘i sağlamak mümkündür. Tüm üretim teknolojilerinde, daha yüksek hassasiyet, daha yüksek maliyettir, bunu azaltmak, mümkün olan yerlerde tolerans genişlemesine gidilmesi önerilmektedir. Tek başına MIM’de ulaşılamayan toleranslara, farklı son işlem prosesleri ile ulaşılabilinir.
Ağırlık ve Boyut: MIM, 100 gr’ın altındaki parçalar için uygundur, en ekonomik çözüm ise 50 gr’ın altındaki uygulamalardır. 250 gr’a kadar olan parçalar da MIM yapılabilir. MIM prosesi için anahtar maliyet yönlendiricisi hammaddedir. MIM, mümkün olan yerlerde, maliyeti azaltmak için parça ağırlığını düşürmeyi önerir. Plastikte olduğu gibi, ağırlığı azaltmak için, iç kısımlarda boşluklar ve güçlendirici kaburgalar, malzeme entegrasyonunu bozmamak kaydıyla kullanılabilir. MIM ile ağırlığı 0,1 gr’ın altındaki mikro boyutlu parçaların üretilmesi de mümkündür. Ağırlık tek başına kısıtlayıcı bir faktor değildir, 250 mm yi geçen ürünler de MIM olarak üretilebilir.
Kesit Kalınlığı: MIM prosesi için, 6 mm’nin altında olan cidar kalınlıkları uygundur. Daha kalın cidarlar mümkündür ancak bu ilave malzeme ve daha uzun proses zamanı gerektirdiği için maliyeti artırır. Alternatif olarak 0,5 mm’den ince cidar kesitlerine ulaşılabilir ancak bu yüksek oranda dizayna bağlıdır.
Üretim Hacmi: Yıllık olarak, binlerle ifade edilebilen düşük hacimlerin yanısıra milyonlarca parça MIM olarak ekonomik bir şekilde üretilebilir. Döküm ve plastikte olduğu gibi, MIM prosesinde de kalıp ve mühendislik yatırımı yapılması zorunludur, bu da düşük hacimli parça üretim prosesinde maliyet açısından önemli bir karar aşamasıdır.
Malzeme: Demir alaşımları, süper alaşımlar, titanyum alaşımları, bakır alaşımları, refrakter metaller, karbürler, seramik ve metal matris kompozitleri gibi çok geniş bir yelpazedeki malzeme MIM prosesinde kullanılabilir. Alüminyum ve bronz gibi demir dışı alaşımların kullanılması teknik olarak mümkündür, ancak, bunların döküm ya da talaşlı imalat yöntemleriyle üretilmesi daha ekonomiktir. Daha detaylı bilgi için lütfen malzeme bölümüne bakınız..
Uygulama Yardımcısı: Indo-MIM, MIM prosesinden daha fazla kazanç elde edilebilmesi için önemli bir destek sağlıyor. Mevcut ürünlerin dizayn değişikliği, malzeme seçimi ile aynı zamanda endüstriyel ürün dizaynı, FEA, hızlı prototipleme ve lazer tarama gibi hizmetlerle destek sağlıyoruz.